Wire fabric mesh is a versatile material that has found applications across a wide range of industries, from construction and architecture to automotive and medical fields. This comprehensive guide will delve into the real-world experiences, expertise, authoritativeness, and trustworthiness associated with wire fabric mesh, aiding your understanding and potentially influencing your selection process for various projects.
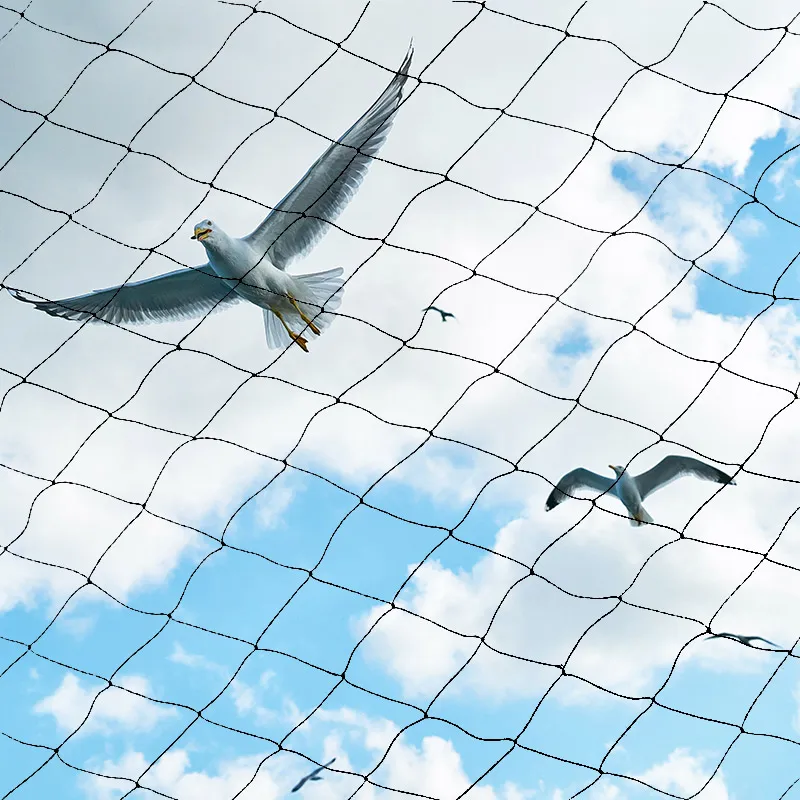
Renowned for its durability and adaptability, wire fabric mesh is composed of interconnected wires forming a grid-like structure. Its primary materials include stainless steel, copper, brass, and galvanized steel, chosen based on the specific requirements of strength, corrosion resistance, or aesthetic appeal. This breadth of choice enhances its usability across both functional and decorative applications.
Professionals with extensive experience recognize the unparalleled strength-to-weight ratio of wire fabric mesh, a critical attribute for construction applications. In reinforced concrete structures, this material acts as a reinforcement agent, providing tensile strength that helps combat cracking and structural failure. The open area between the wires also offers excellent binding properties with concrete, ensuring a secure and reliable support matrix.
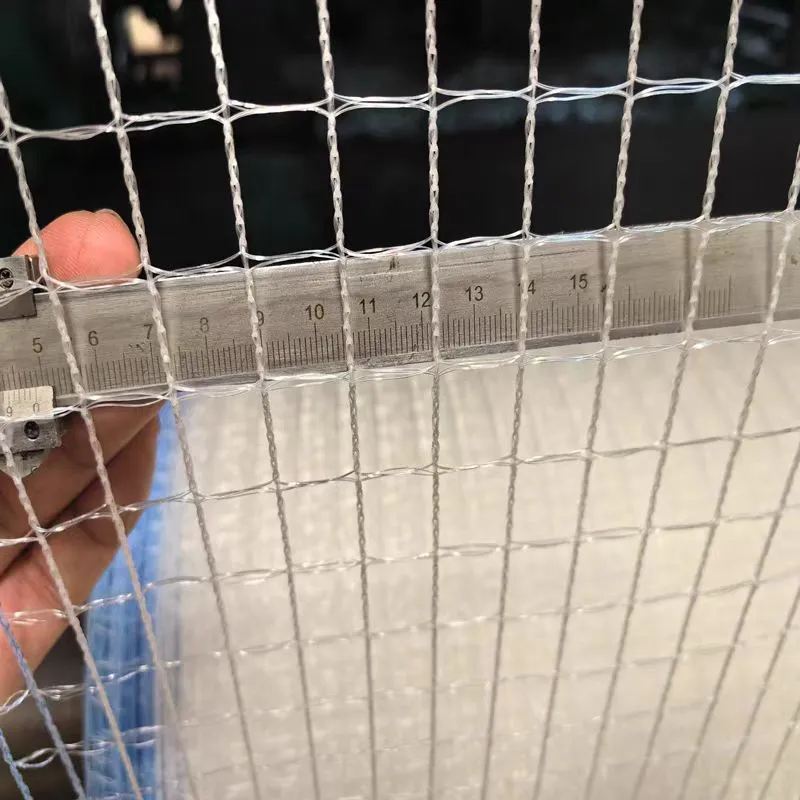
In the realm of architecture, wire fabric mesh brings not only physical strength but also aesthetic flexibility. With a variety of weaving patterns and customizable apertures and wire diameters, architects and designers utilize this mesh to create dynamic façades, interior partitions, and sunshades, merging functionality and visual appeal seamlessly. Credible examples of such applications can be found in iconic structures worldwide, where mesh contributes both to energy efficiency and modern design aesthetics.
The automotive industry benefits from wire fabric mesh through its application in filtration systems and protective barriers. The precision in weave and material consistency ensures that it meets the stringent standards required for filtering contaminants from fuel or air, thus enhancing engine efficiency and longevity. Likewise, wire mesh's role as a protective grille in automotive front ends is essential for safeguarding radiators while allowing sufficient airflow, a delicate balance that speaks to the material's engineering excellence.
wire fabric mesh
In medical environments, trust in wire fabric mesh is paramount. Manufactured under strict quality control standards, these meshes are used in surgical implants, such as hernia repair devices. The biocompatibility of medical-grade wire mesh ensures that it integrates safely into the human body, facilitating healing and providing long-term relief. Surgical teams depend on the reliable performance of these meshes, cementing their status as a vital component in modern medicine.
Authoritativeness in the field of wire fabric mesh extends to the involvement of standards organizations such as ASTM (American Society for Testing and Materials) and ISO (International Organization for Standardization). These bodies set international standards that govern the manufacturing process, ensuring the consistent quality and safety of wire mesh products. Compliance with these standards is a non-negotiable requirement for manufacturers aiming to reach a global market, and it underscores their commitment to maintaining high product standards.
From an expertise standpoint, the production of wire fabric mesh involves intricate processes including drawing, weaving, welding, and finishing. Advanced machinery enables precise control over these processes, resulting in products that meet the precise technical specifications demanded by diverse industries. The expert handling and monitoring during these stages ensure that the final product not only meets but often exceeds user expectations.
The trustworthiness of wire fabric mesh products is often solidified by extensive testing, including stress tests, corrosion resistance assessments, and load-bearing evaluations.
These tests simulate real-world conditions and confirm the reliability of the mesh over extended periods. For end-users, this testing translates into confidence that the chosen product will perform as expected, without premature deterioration or failure.
In conclusion, the application of wire fabric mesh across multiple sectors is a testament to its unmatched versatility and functionality. Its evolution over time, continually refined through experience, expertise, and adherence to authoritative standards, has secured its place as a material of choice among engineers, architects, automotive designers, and medical professionals. As industries grow and demands become increasingly complex, wire fabric mesh is poised to remain a key player, underpinned by its inherent qualities of reliability, adaptability, and strength.