In the world of filtration systems and material processing, the 500 micron nylon mesh stands out as a remarkable tool known for its durability and efficiency. This type of mesh has found application in various industries due to its unique properties, making it invaluable for professionals who require precise filtration capabilities.
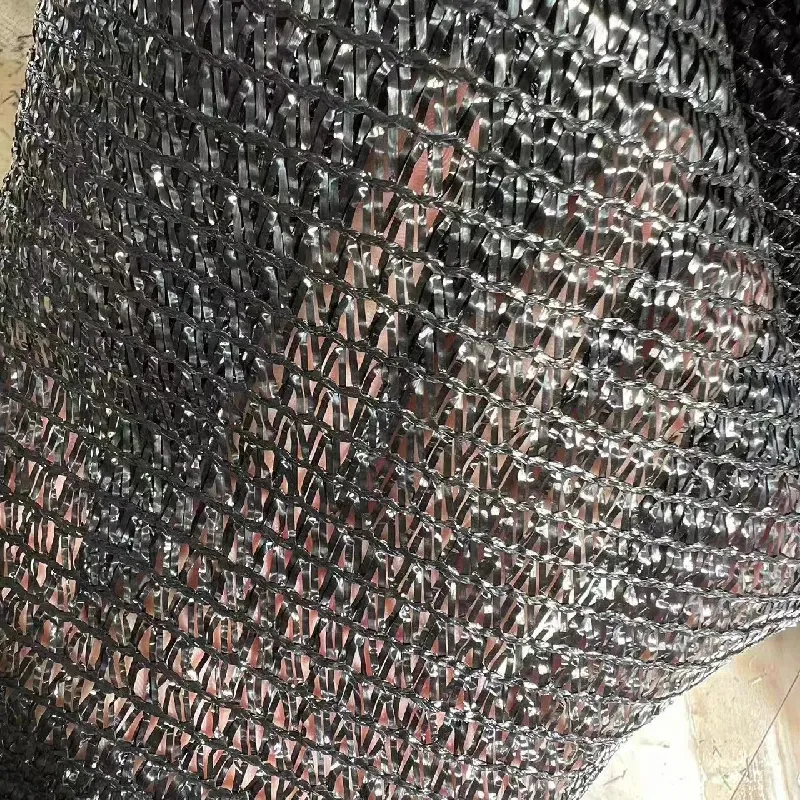
Manufactured from high-quality nylon, the 500 micron mesh boasts exceptional resilience and longevity, enabling it to withstand rigorous use over time. It offers a balance between flexibility and robustness, which ensures it can be employed in demanding environments without easily succumbing to wear and tear.
The mesh's micron rating refers to the size of the openings within the material.
At 500 microns, it effectively filters out larger particles while allowing liquids and smaller particulates to pass through. This makes it particularly favorable for industries dealing with viscous fluids or where larger debris needs to be separated from finer components. For example, in the brewing industry, this specific mesh size is ideal for separating grains from wort, ensuring a smoother brewing process and a cleaner end product.
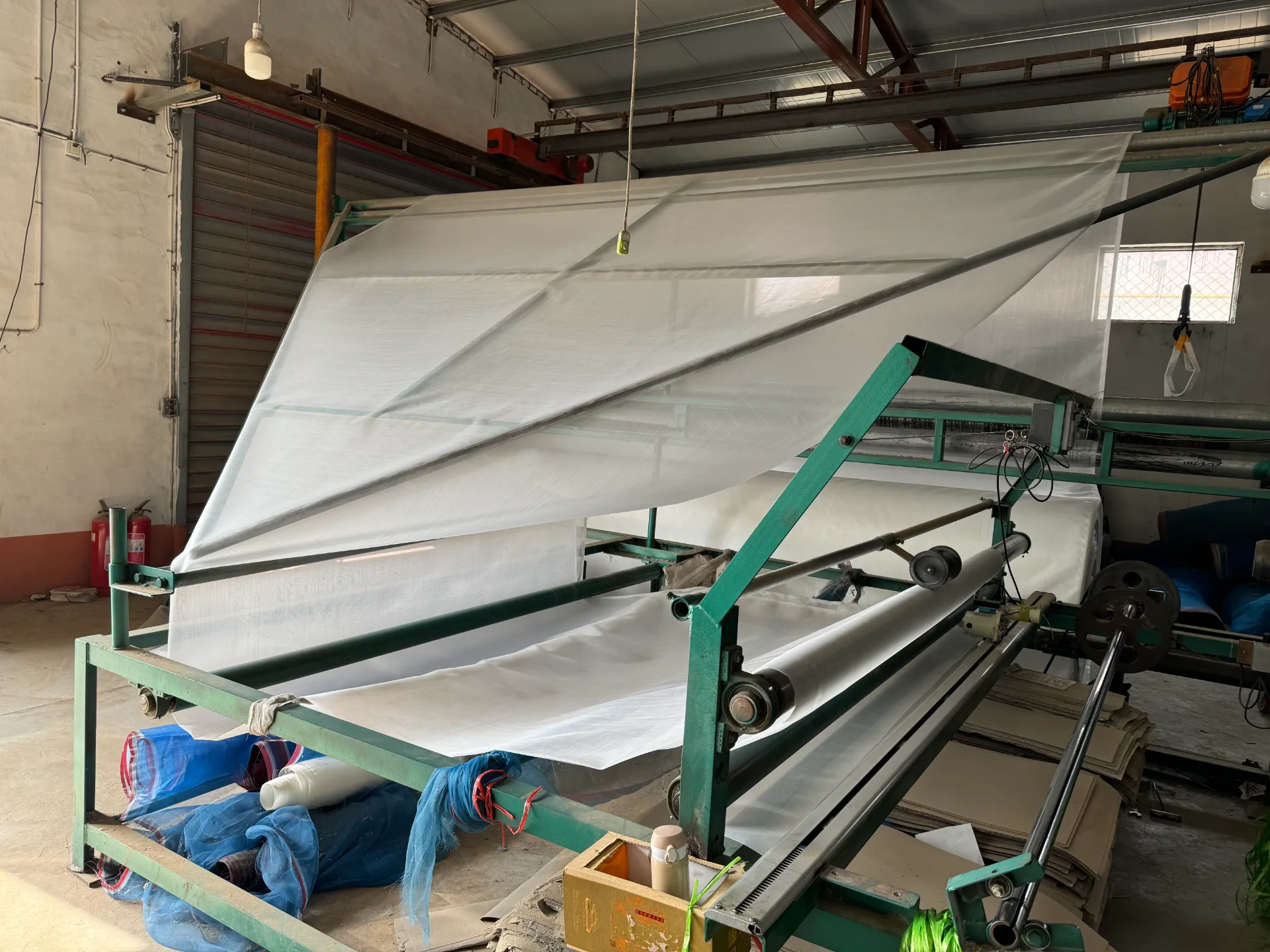
Engineers and plant managers who use 500 micron nylon mesh appreciate its versatility. Because nylon is resistant to many chemicals, it can be used in a range of industrial applications — from water treatment to chemical processing plants — without degrading or compromising the integrity of the filtration system. This chemical resistance also contributes to the mesh's longevity, reducing the need for frequent replacements and thus lowering operational costs.
Precision and efficiency are critical in industrial settings, and the uniformity of the nylon mesh guarantees consistent filtration results. Each fiber is woven meticulously, ensuring the gap sizes remain consistent across the entire mesh surface. This high level of precision means less downtime and mistakes in industrial processes, ultimately leading to more efficient production cycles and higher quality end products.
500 micron nylon mesh
From a technical perspective, utilizing 500 micron nylon mesh also minimizes clogging, a common issue with finer meshes. Its design allows for larger particulate capture without the risk of blocking the entire system. This quality is particularly advantageous in circumstances where flow rates are crucial, and maintaining a steady filtration process is of the utmost importance.
For professionals seeking certifications or assurance of quality, 500 micron nylon mesh often meets or exceeds industry standards. Manufacturers committed to excellence typically subject their products to rigorous testing, ensuring that each mesh can withstand specified pressures and environmental conditions. This attention to quality helps build trust with clients who rely on these materials for critical operational components.
Moreover, the ease of installation and maintenance associated with nylon mesh products enhances their attractiveness. The material's inherent flexibility ensures that it can be tailored to fit different system specifications, and its resilience reduces maintenance demands. Cleaning nylon mesh is a straightforward process, further reinforcing its practical appeal and allowing for repeated use without affecting its performance.
For sectors prioritizing sustainable solutions, nylon mesh can often be recycled or repurposed, promoting environmental responsibility. This factor can be a significant selling point for businesses committed to sustainable practices, enabling them to integrate effective filtration solutions with their broader environmental targets.
The adoption of 500 micron nylon mesh in various industrial applications is a testament to its effectiveness and reliability. With continuous innovations in production techniques and material sciences, the potential applications and efficiencies of nylon meshes are likely to expand, offering even more refined solutions to complex filtration challenges. By leveraging the robust features and flexibility of 500 micron nylon mesh, industries can enhance their operational efficacy, achieving precise and reliable separation processes essential for maintaining high standards in production and output.