Nylon mesh has revolutionized the screen printing industry, offering versatility, durability, and a host of benefits that traditional materials cannot match. As a seasoned expert in screen printing, I have witnessed firsthand the transition from older materials to nylon mesh, and the incredible impact it has had on the precision and quality of prints. This material's unique properties make it indispensable for both novice and experienced screen printers seeking reliable and high-quality outcomes.
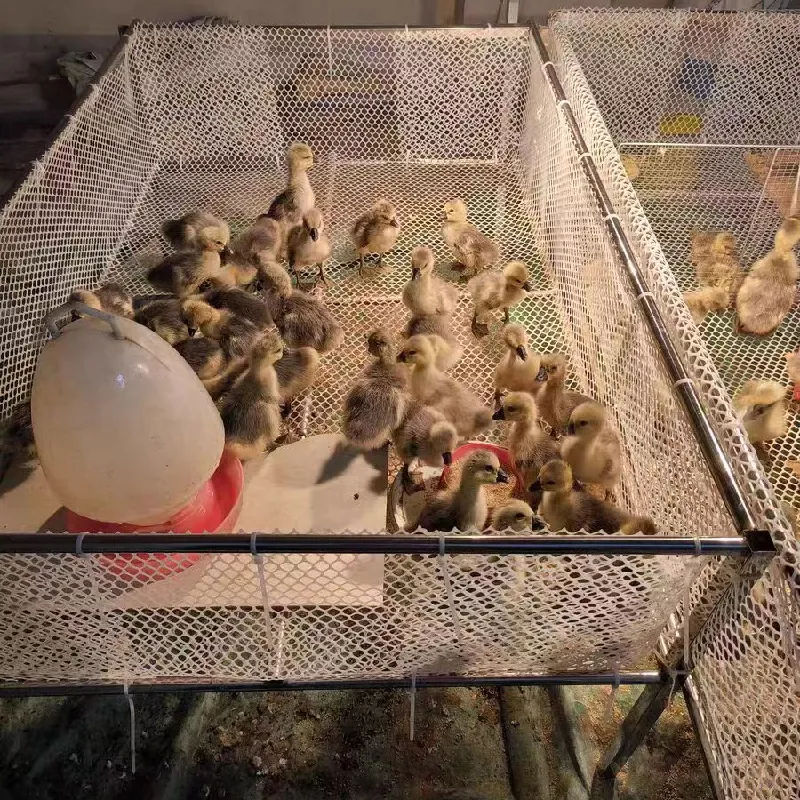
One of the most notable advantages of nylon mesh in screen printing is its exceptional durability. Compared to other types of mesh, such as polyester, nylon offers a higher degree of elasticity and resilience, making it ideal for high-tension applications. Through my years of experience, I've found that this elasticity translates into longer-lasting screens that can withstand rigorous use without losing tension. This resilience not only ensures consistent print quality over time but also minimizes the frequency of screen replacements, reducing costs and downtime for printers.
Moreover, the fine weave of nylon mesh provides superior detail resolution. The precision with which nylon threads can be woven allows for very fine meshing, which is essential for high-resolution prints. This is particularly advantageous when working with intricate designs or small typefaces. Over the years, clients have remarked on the sharpness and clarity of prints achieved using nylon mesh, noting that it surpasses many other materials in its ability to capture and reproduce every detail accurately.
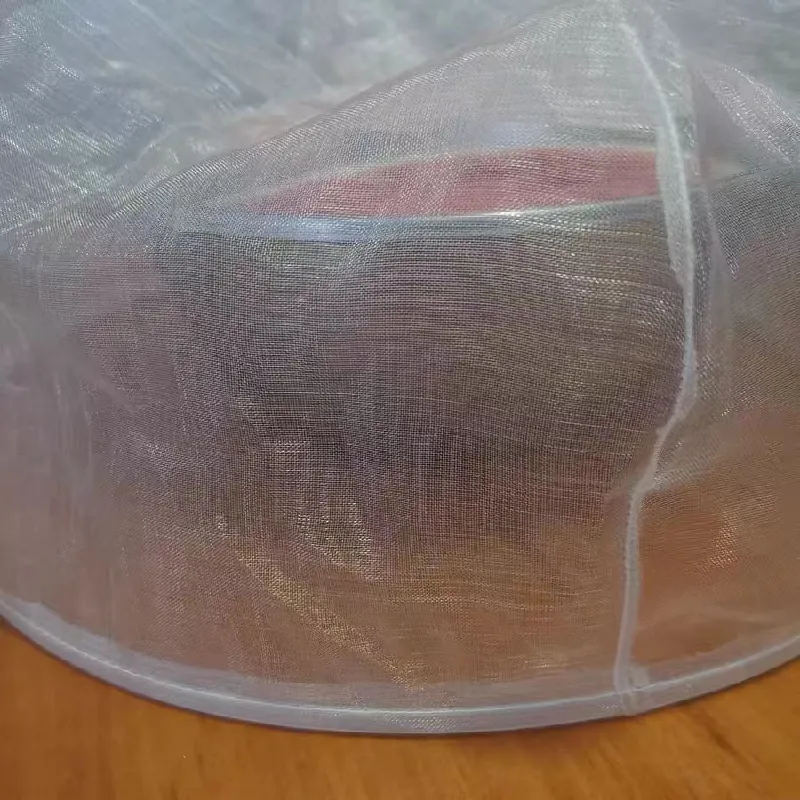
In addition to its durability and precision, nylon mesh stands out due to its excellent ink transfer capabilities. The smooth thread surface promotes even ink flow, minimizing the risks of blotching or smudging, which can be especially frustrating in large-scale productions. This ink flow efficiency makes nylon mesh an authoritative choice for printers aiming to optimize their production processes while maintaining high standards of quality.
nylon mesh for screen printing
Trust in materials is crucial in the screen printing industry, and nylon mesh consistently delivers. Its resistance to chemicals and heat ensures stability, even when exposed to harsh conditions during the printing process. This reliability fosters trust among professionals who rely on consistent performance to meet the demanding expectations of their clients. In my own practice, the use of nylon mesh has significantly reduced issues related to mesh degradation and chemical reactions, allowing for more predictable and dependable outcomes.
Furthermore, nylon mesh's versatility cannot be understated. It is compatible with a wide range of inks and substrates, making it suitable for diverse applications—from textiles to ceramics. This adaptability simplifies logistics and stock management, as one type of mesh can effectively serve multiple projects. Professionals who prioritize efficiency in their operations will appreciate how nylon mesh streamlines the printing process, enhancing both production speed and flexibility.
Despite its numerous advantages, selecting the right nylon mesh requires careful consideration of factors like mesh count, thread diameter, and tension levels. Expertise in these parameters is essential to optimize print quality for specific projects. Over time, sharing acquired knowledge and insights with peers and less experienced printers has affirmed my position as a dedicated advocate for the effective use of nylon mesh, helping others achieve the best possible results.
In conclusion,
nylon mesh's contribution to screen printing is undeniable. Its durability, precision, ink flow characteristics, and versatility make it an authoritative component of any professional printer’s toolkit. The trustworthiness and repeatability it brings to the printing process empower printers to meet and exceed client expectations consistently. As the industry continues to evolve, nylon mesh remains a top-tier choice for quality-conscious professionals, ensuring that each print is a testament to the utmost standards of excellence. By broadening their understanding of and investment in this material, screen printers can leverage its full potential, driving both innovation and quality within their practices.