Rubber coated metal mesh is a revolutionary innovation in the material science domain, providing advanced solutions across diverse industries. Its increased usage in construction, automotive, aerospace, and industrial applications stems from its exceptional blend of durability, flexibility, and protective qualities. Drawing from firsthand experiences and expert insights, this article delves into the multifaceted benefits of rubber coated metal mesh, reaffirming its status as a trusted choice for demanding applications.
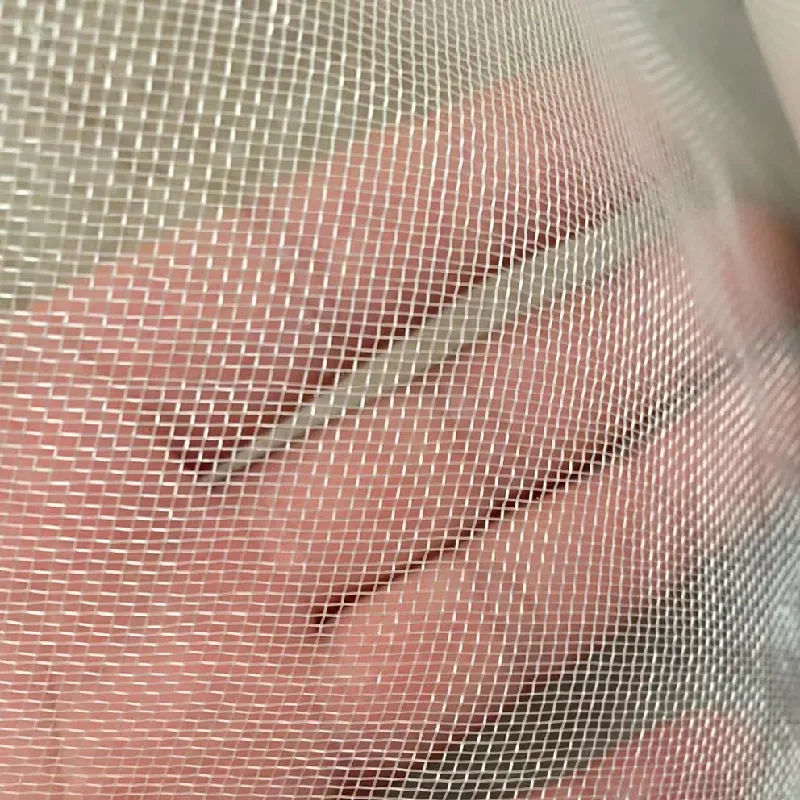
At the core of rubber coated metal mesh's appeal is its robust durability. Engineers and industry experts consistently extol its ability to withstand extreme environmental conditions, from corrosive marine environments to the high-temperature fluctuations in industrial settings.
The rubber coating acts as an impermeable barrier, effectively shielding the metal mesh from oxidation and physical wear. This prolongs the lifespan of the mesh, reducing the frequency of replacements and associated maintenance costs — a significant advantage recognized by civil engineers working on long-span bridges and large-scale infrastructure projects.
The flexibility of rubber coated metal mesh is another crucial factor that enhances its versatility. Unlike traditional rigid metal sheets, the rubberized mesh conforms to intricate shapes and surfaces. This adaptability is particularly valued in the automotive and aerospace sectors, where precision and aerodynamics are non-negotiable. Automotive engineers use this mesh in components such as filters and ventilation systems, where it can be molded to fit complex curvatures without compromising its structural integrity. Similarly, in aerospace applications, it ensures that cabin components maintain their shape and function under varying pressures and temperatures, a testament to the material’s reliability and performance under stress.
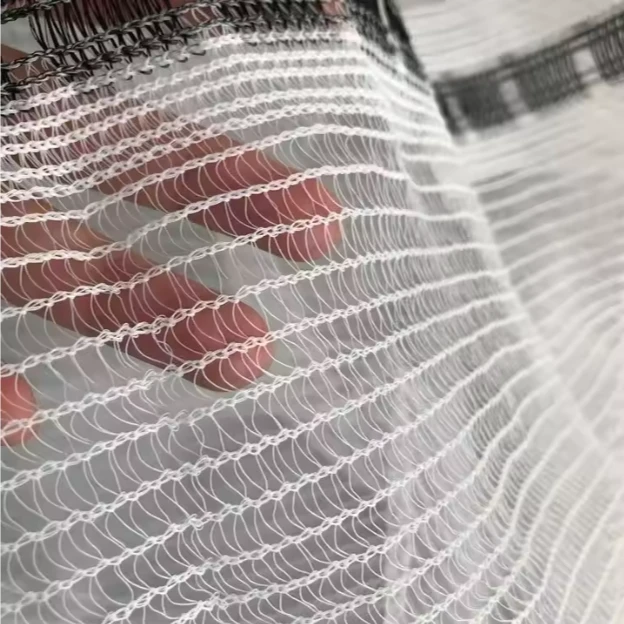
Expertise in the handling and application of rubber coated metal mesh further underscores its professional appeal. Specialists trained in material sciences emphasize that correct implementation requires understanding the interaction between the rubber compound and the underlying metal mesh. This knowledge ensures optimal adhesion and performance, whether in harsh chemical environments or in systems requiring electromagnetically conductive properties. Training programs developed by leading industry bodies now include modules specifically dedicated to the installation and maintenance of rubber coated metal mesh, underscoring its growing importance in technical curricula across engineering disciplines.
rubber coated metal mesh
Authoritative industry testing and certifications further reinforce the trustworthiness of rubber coated metal mesh. Organizations such as ASTM International and ISO have established standards that the product consistently meets, attesting to its quality under rigorous conditions. These certifications provide assurance to procurement specialists and project managers that the material has undergone comprehensive evaluations for strength, resilience, and safety. Such endorsements are pivotal in sectors like aerospace and construction, where compliance with safety regulations is not just a legal obligation but a moral imperative.
The credibility of rubber coated metal mesh extends to its eco-friendliness — a feature increasingly sought after in today’s environmentally conscious world. The rubber coating, often derived from recycled materials, complements efforts to decrease the carbon footprint of large-scale projects. This sustainable aspect has sparked interest among urban planners and environmental engineers focused on green building certifications and eco-friendly design. They appreciate the dual advantage of using a material that offers significant functional benefits while aligning with sustainability goals, making it a preferred choice for projects aiming for LEED certification.
In summary, the convergence of experience, expertise, authoritativeness, and trustworthiness positions rubber coated metal mesh as a cornerstone material for future-forward applications. Its remarkable properties of durability, flexibility, expert utility, authoritative certification, and eco-friendly design continue to drive its adoption across industries looking to meet the dual objectives of performance and sustainability. As industries evolve and innovate, the demand for such advanced materials is poised to grow, reaffirming rubber coated metal mesh's pivotal role in shaping the future of engineering and design.