For industrial applications requiring optimal efficiency and purity, the choice of filtration equipment can significantly impact operational success. The stainless steel inline strainer, with its robust design and versatile applicability, is a standout component in many engineering and processing environments.
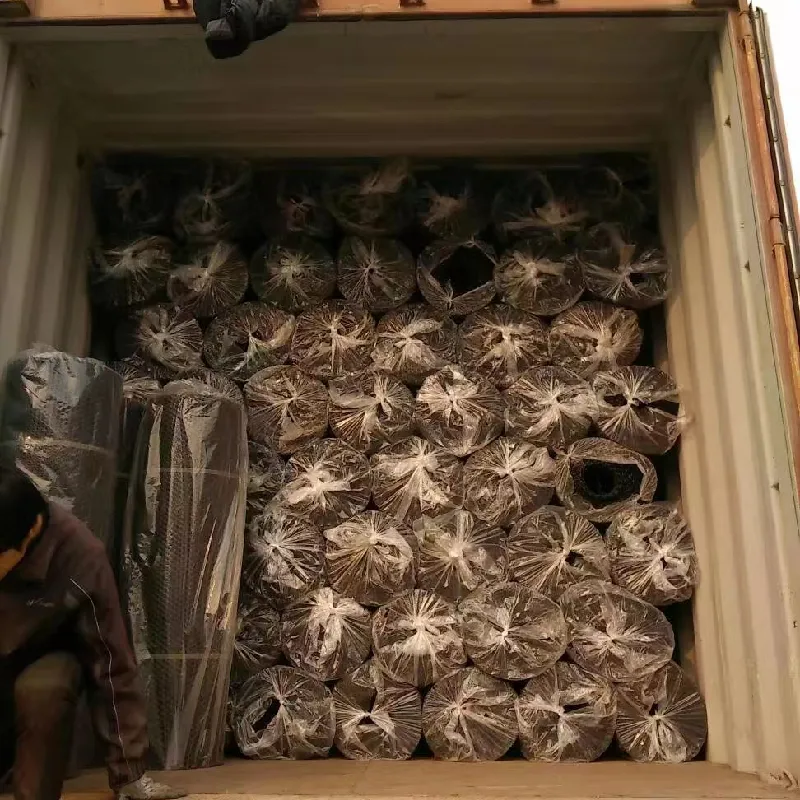
Stainless steel inline strainers are engineered for use in a variety of sectors, including chemical processing, food and beverage production, and pharmaceuticals. These devices effectively remove debris from liquids, ensuring smooth operations and protecting downstream equipment from potential clogs or damage. The material construction of stainless steel is especially advantageous due to its corrosion-resistant properties, making it ideal for both aggressive and hygienic applications.
In industries where safety and compliance are paramount, stainless steel inline strainers offer unmatched reliability. Unlike plastic or lesser-grade metal alternatives, stainless steel can withstand extreme temperatures and pressures, maintaining structural integrity. This durability is critical in maintaining operational uptime, as strainers are less likely to succumb to wear and require frequent replacements. This longevity not only reduces downtime costs associated with maintenance but also ensures a consistent quality of the filtered product.
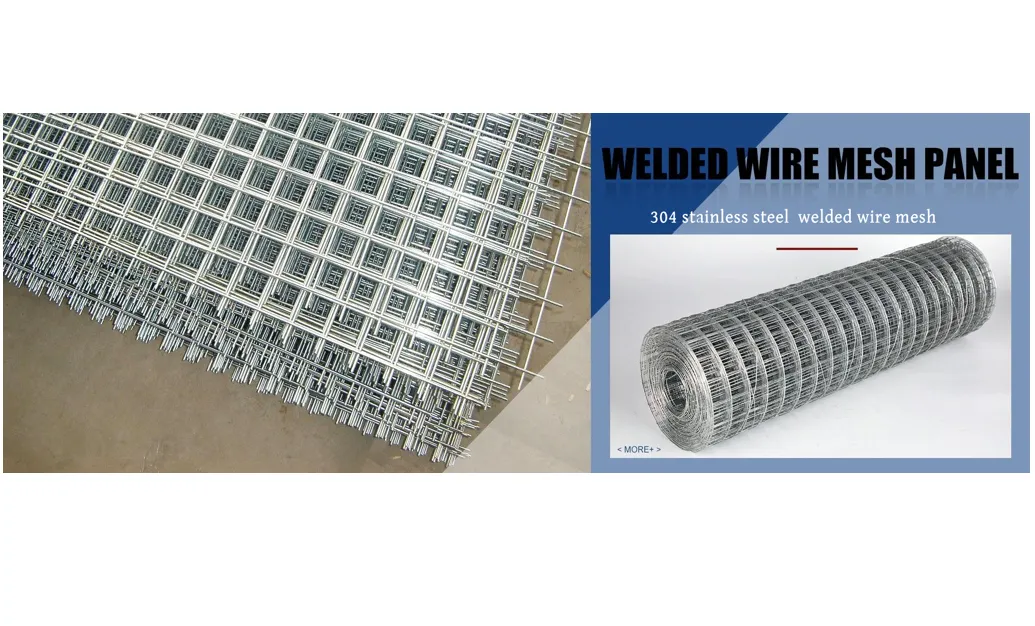
From an operational perspective,
the expertise involved in choosing the right inline strainer cannot be overstated. Process engineers and plant managers often assess factors such as flow rate, particle size, and fluid characteristics to determine the most suitable strainer design. The high surface area and customizable mesh sizes available in stainless steel inline strainers allow for precise filtration tailored to specific industry needs. This ensures that processes run efficiently, with minimal interruption and contamination risk.
Moreover, the authoritativeness of utilizing stainless steel inline strainers is reflected in their regulatory approval across multiple industries. Many strainers comply with standards set by organizations such as the FDA and European Hygienic Engineering and Design Group (EHEDG), underscoring their suitability for use in environments where hygiene standards are stringent. The assurance of quality and conformity to these standards fosters trust among end-users, enhancing a company's reputation and leading to better business relationships.
stainless steel inline strainer
Real-world experience with stainless steel inline strainers highlights their ease of integration into existing systems. Their design allows for straightforward installation in pipelines, tanks, or other processing equipment without necessitating extensive modifications. This adaptability is a key feature for industrial facilities aiming to upgrade their filtration capabilities without incurring substantial overhaul costs.
Another significant aspect of stainless steel inline strainers is their role in sustainability. As industries move towards environmentally friendly practices, the recyclability of stainless steel supports such initiatives. The ability to recover and reuse this material contributes to a circular economy, reducing waste and environmental impact—a priority for many organizations today.
Case studies from various sectors further demonstrate the trustworthiness and effective deployment of stainless steel inline strainers. For example, in the dairy industry, these strainers are indispensable in ensuring the removal of unwanted particulates while preserving product purity, which directly influences taste and consumer safety. In chemical processing, the robust nature of stainless steel provides peace of mind when handling corrosive fluids, an essential factor in maintaining safety and product integrity.
In conclusion, the stainless steel inline strainer is not just a filtration tool but a critical component fostering operational excellence. Its expertise in design, authoritativeness through compliance, and proven reliability exhibit remarkable value across industries. As companies strive to optimize processes and adhere to stringent industry standards, investing in such reliable equipment can lead to sustainable success, ensuring products are pure, operations are smooth, and businesses build trust with their stakeholders. Experience and case studies continually affirm their standing as a pivotal element in modern industrial operations, making them an indispensable choice for businesses targeting efficiency and excellence in their filtration processes.