Welding fence wire effectively requires both skill and the right equipment, making it pivotal in securing properties with resilience and strength. As an integral component of many security barriers, welding the fence wire correctly can mean the difference between a structure that stands the test of time and one that falls short of expectations.
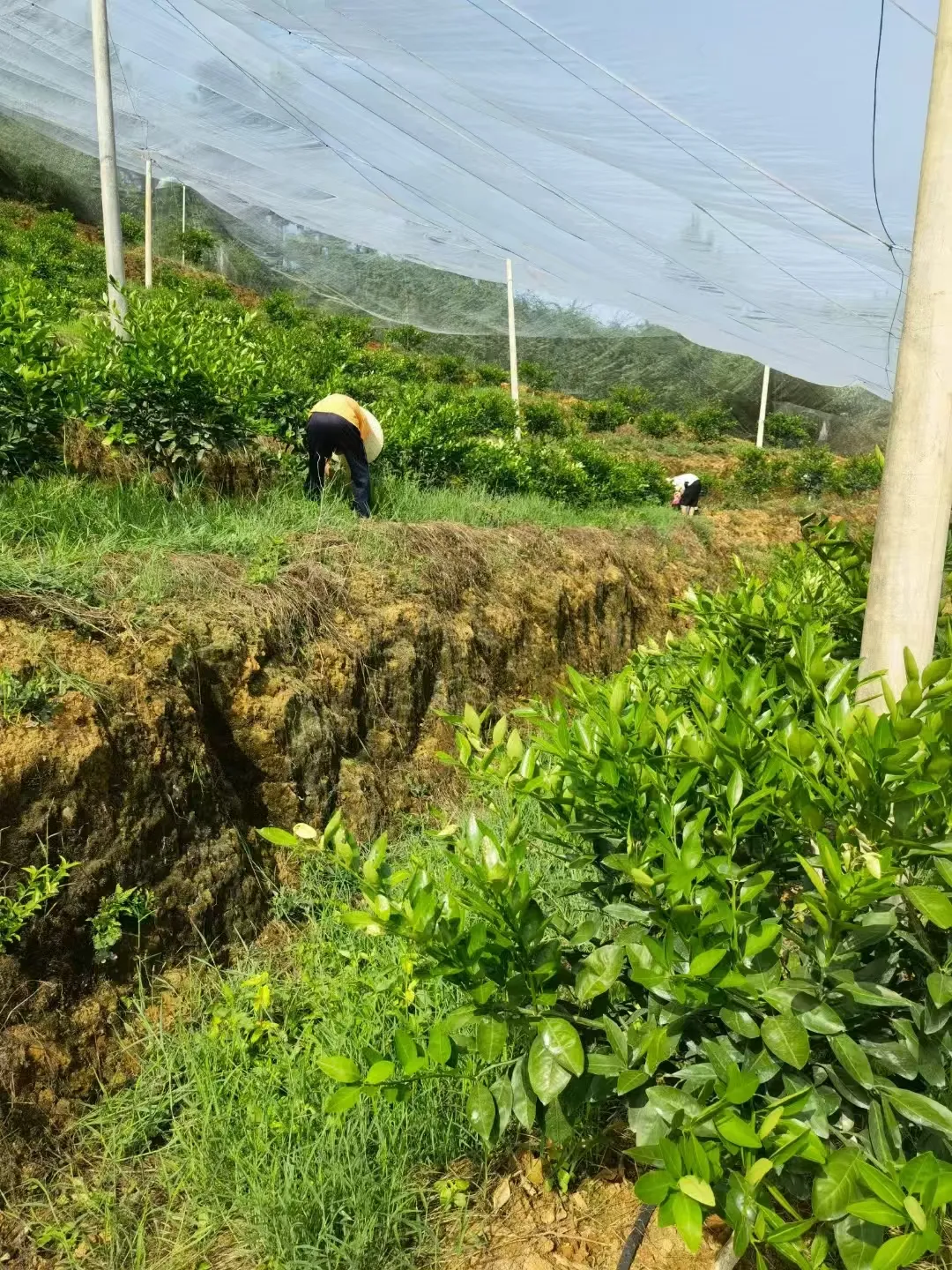
With years of experience in the field, my journey into welding fence wire started with understanding the various materials at hand. Most commonly, these wires are made from mild steel, galvanized steel, or stainless steel. Each type has its unique properties; for instance, galvanized steel is renowned for its resistance to rust and corrosion, making it a favorite for outdoor applications. Stainless steel, on the other hand, offers unparalleled strength and an aesthetically pleasing finish, albeit at a higher cost.
One crucial aspect of welding fence wire is selecting the right welding technique. The two prevalent methods are MIG (Metal Inert Gas) welding and TIG (Tungsten Inert Gas) welding. MIG welding is often the go-to choice for its speed and ease, making it ideal for large projects where efficiency is key. It involves feeding a wire electrode through a welding gun and into the weld pool, combining the base metals. Conversely, TIG welding, while slower, is often called upon for projects requiring more precision and a cleaner finish.
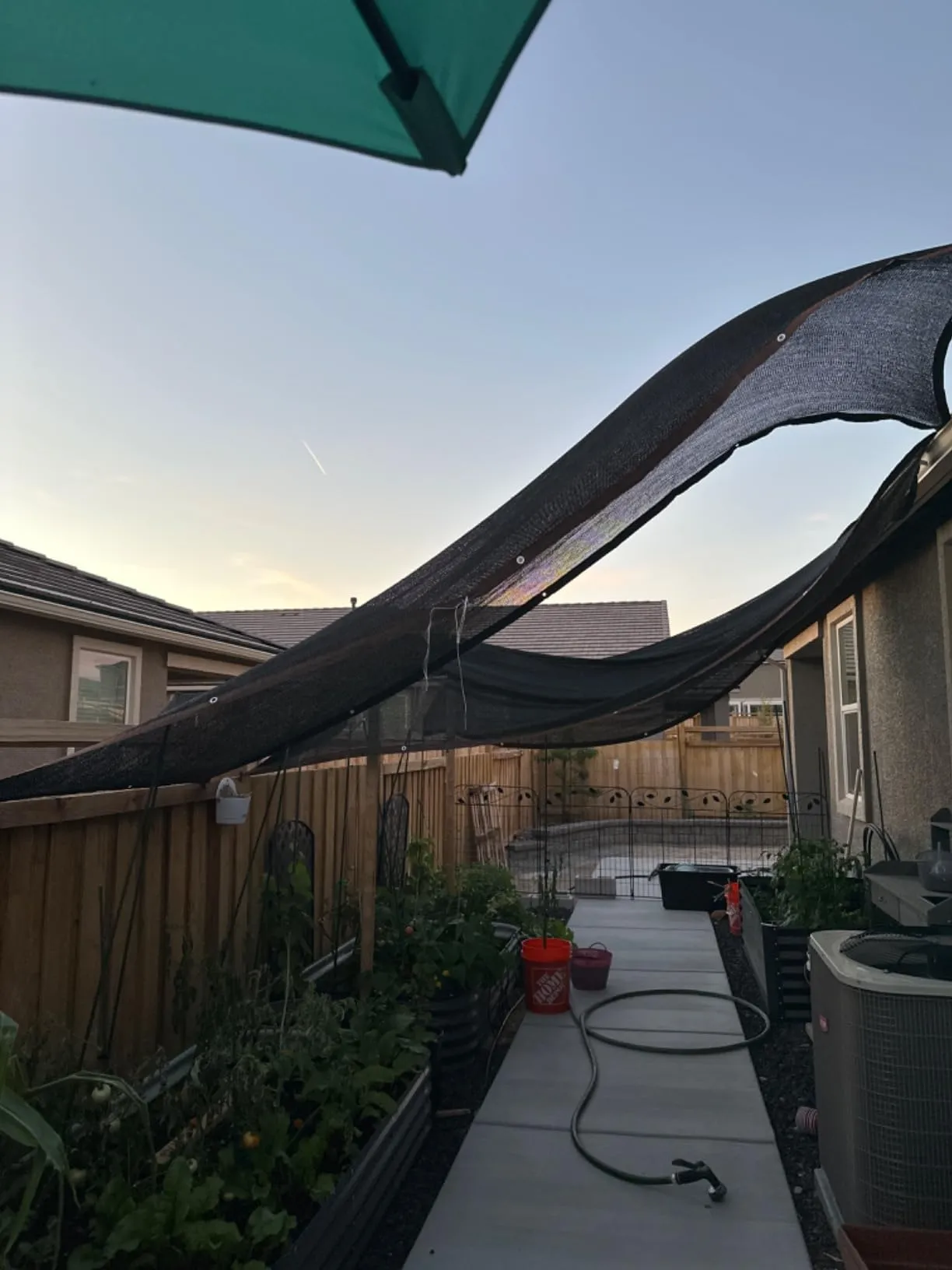
Professionalism in welding also calls for meticulous attention to safety protocols. This cannot be overstated as the welding process inherently involves risks such as intense UV radiation, high temperatures, and the potential for electric shocks. Wearing appropriate protective gear, including welding helmets, gloves, and aprons, is non-negotiable. Moreover, ensuring proper ventilation is vital to avoid inhaling harmful fumes.
In my professional experience, one often overlooked yet critical factor is the preparation of the area to be welded. Cleaning the fence wire of any debris or coatings is essential to ensure a strong and clean weld. Using a wire brush or grinder to remove any surface rust or paint can make a significant difference in the weld quality. Proper alignment of the wires prior to welding is also crucial, as it impacts not only the aesthetic appeal but also the structural integrity of the fence.
welding fence wire
Understanding wire gauge and tension is another area where expertise is non-negotiable. The wire gauge affects the strength and flexibility of the fence. Thicker gauges typically offer more strength but require more skill and higher amperage settings for proper welding. Maintaining consistent tension throughout the welding process ensures that the fence remains taut and functional.
In terms of authority and trust, adhering to industry standards and guidelines sets the benchmark for quality. Organizations such as the American Welding Society (AWS) provide invaluable resources and certifications that attest to a welder’s skill and knowledge. Being certified not only enhances credibility but also assures clients of a professional approach to their projects.
Investing in high-quality welding equipment can significantly influence the outcome of the welding process. A reliable welding machine that includes voltage control and adequate power output is pivotal for seamless operation. Likewise, regular maintenance of equipment ensures consistent performance and longevity, thereby enhancing trustworthiness and dependability in workmanship.
In conclusion, welding fence wire is a specialized skill that combines experience, expertise, and a commitment to quality and safety. Each project presents unique challenges, but with the right approach and adherence to best practices, one can achieve a secure and durable fencing solution. As the dynamics of security solutions evolve, so does the technology and techniques in welding, making continual learning and adaptation an essential part of a welder's professional journey.