The weld mesh manufacturing machine has emerged as a pivotal innovation in the industrial sector, reshaping how weld mesh is produced in today’s competitive markets. As the demand for durable and cost-effective fencing solutions increases, businesses are turning towards sophisticated machinery that ensures precision, efficiency, and reliability. This article delves deep into the multifaceted world of weld mesh manufacturing machines, emphasizing their operational mechanics and the paramount benefits they bring to the table.
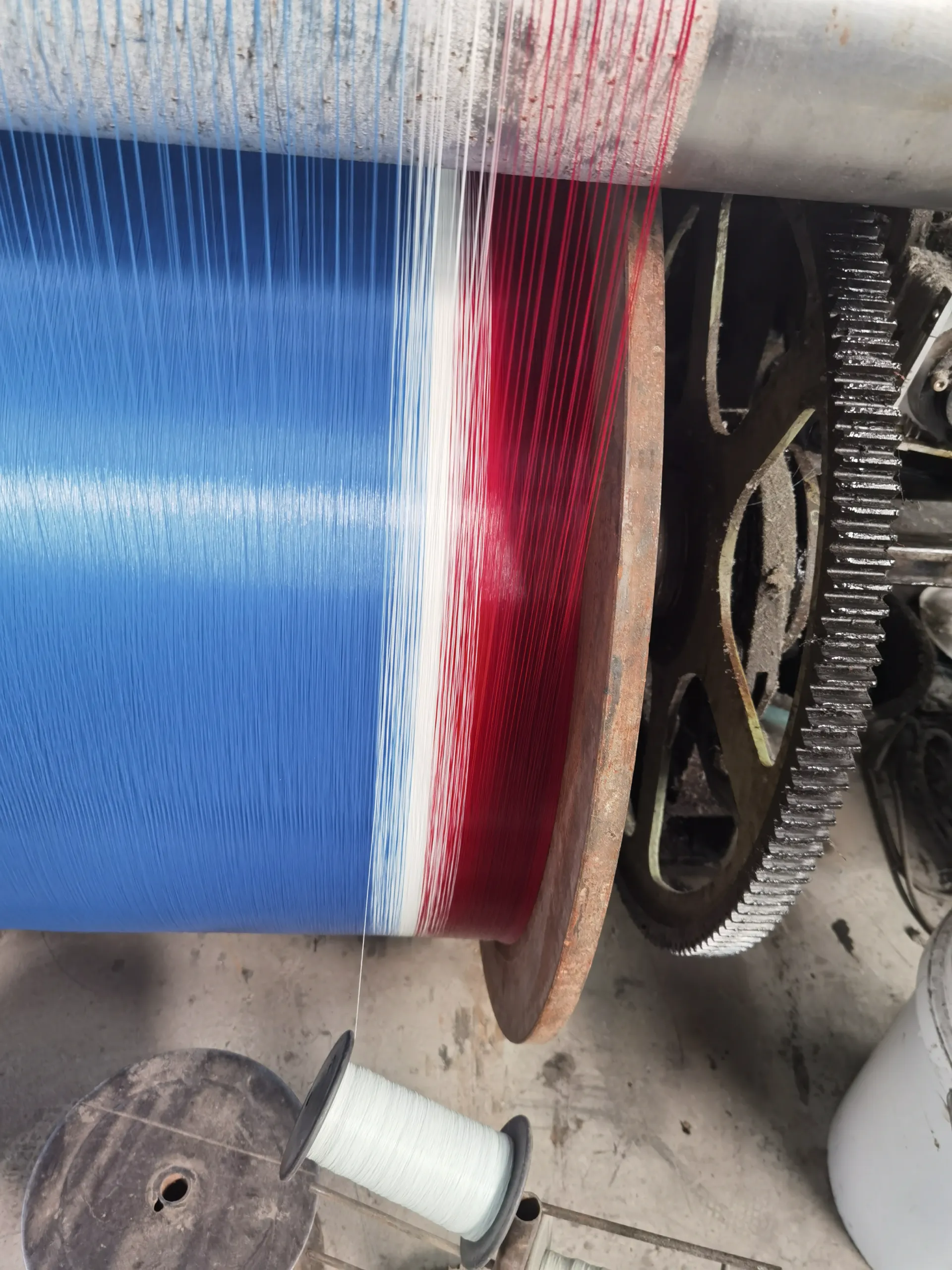
Understanding the operational prowess of a weld mesh manufacturing machine requires a look into its integral components. These machines typically feature an automated wire feeding system, precision welding electrodes, and an advanced control interface. The automated wire feeding ensures that wires are consistently supplied at the right tension, minimizing manual intervention. This, combined with high-precision welding electrodes, guarantees uniformity and strength in the mesh produced. The control interface, often equipped with the latest software, allows operators to adjust weld patterns, mesh sizes, and welding speeds, making it highly adaptable to diverse production requirements.
From an expertise standpoint, weld mesh manufacturing machines are engineered to enhance efficiency and reduce wastage. Traditional methods often suffer from material wastage and inconsistent outputs. However, with modern machines, the accuracy of welds and the consistency of mesh alignment significantly improve production quality. Engineers skilled in operating these machines emphasize the importance of regular maintenance checks and software updates. These actions not only prolong the life of the machine but also ensure that it operates at optimal performance, maintaining the highest standards of output.
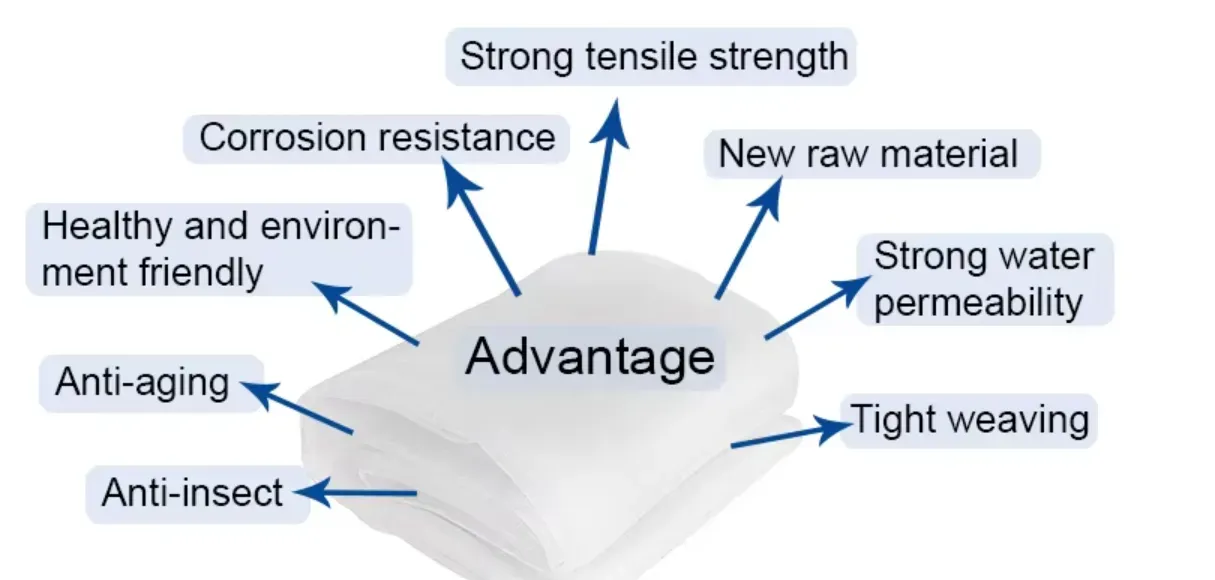
In terms of authoritativeness and trustworthiness, leading manufacturers of weld mesh machines have established rigorous standards and certifications to ensure product quality. These industry giants often have decades of experience and are committed to innovation and customer satisfaction. Certifications from globally recognized bodies serve as a testament to the reliability and safety of the machines, instilling confidence among buyers. Furthermore, expert operators are regularly trained and certified, ensuring that they are updated with the latest technological advancements and safety protocols.
weld mesh manufacturing machine
Real-world experience with weld mesh manufacturing machines consistently highlights their economic and operational advantages. Businesses that have integrated these machines into their production lines report a marked increase in output and a notable reduction in overhead costs. The automation and precision of these machines translate to fewer man-hours and minimize the error rate, leading to substantial cost savings over time. Moreover, their versatility in handling different wire materials and mesh specifications makes them indispensable in industries ranging from construction to agriculture.
Trust in these machines is further cemented by their robust construction and the support offered by manufacturers. Reliable after-sales services ensure that any operational hiccups are swiftly addressed, decreasing downtime and maintaining productivity levels.
This reliability is a crucial factor for businesses aiming to meet tight deadlines and customer expectations.
In conclusion, weld mesh manufacturing machines stand as a testament to technological progress in the industrial sector. Their design, efficiency, and operational benefits make them an invaluable asset for any business aiming to stay ahead in the competitive market landscape. With a solid foundation of real experience and stringent adherence to quality and safety standards, these machines continue to uphold their position as the backbone of modern mesh production.