As the automotive industry continues to evolve, there is an ever-increasing demand for materials that not only simplify manufacturing processes but also enhance the performance and safety of vehicles. Among these materials, wire mesh stands as an exemplar of versatility and efficiency that has firmly established its footprint in the automotive domain. This article explores the nuanced role wire mesh plays in the automotive industry, detailing its applications, benefits, and the reasons behind its growing adoption.
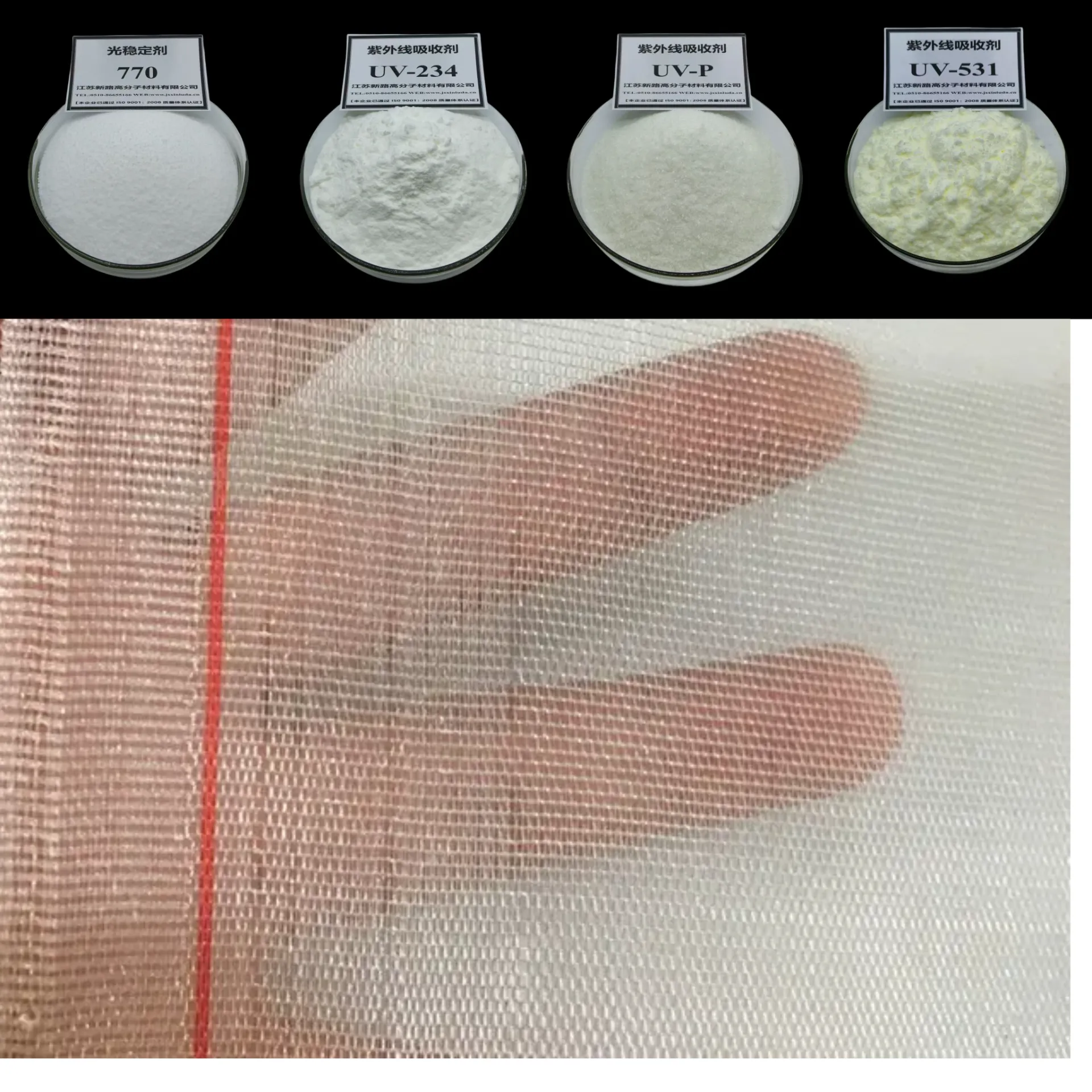
Wire mesh, made from a variety of metals such as stainless steel, aluminum, and copper, is a relatively simple material at first glance. However, its design — a network of interwoven metal wires — provides complex benefits that align closely with the demands of modern automotive engineering.
In the automotive sector, one of the most prominent uses of wire mesh is in vehicle filtration systems. Here, it acts as both an air and fluid filter, optimizing engine performance. The open structure of wire mesh permits superior air flow through the engine's intake, thereby enhancing the engine's efficiency and power output. Unlike traditional paper filters, wire mesh can withstand higher temperatures and does not degrade as easily, thus extending the life of the component and reducing maintenance costs.
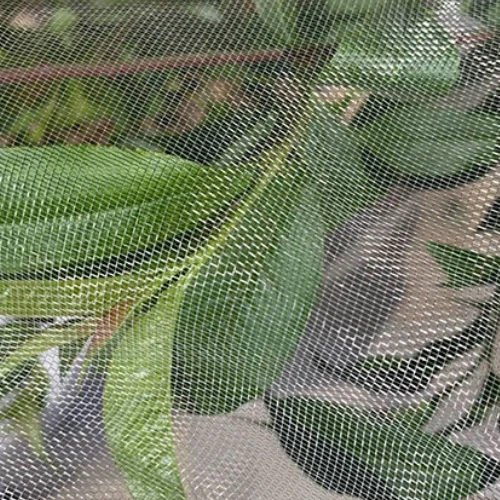
Furthermore,
wire mesh serves as an essential component in automotive safety. It is used in the construction of airbags to ensure their rapid and reliable deployment. During a collision, the mesh aids in the precise dispersion of the chemical reaction needed to inflate the airbags quickly and effectively, a task that requires both rapid response and tensile strength, inherent characteristics of wire mesh.
In the realm of automotive design, wire mesh offers aesthetic and practical solutions. Car manufacturers leverage it for the distinctive grilles and vents on vehicles, which not only contribute to the sleek, aggressive look of modern vehicles but also play a role in aerodynamics and cooling systems. This dual role enhances the vehicle's visual appeal while simultaneously ensuring efficient thermal regulation of the engine and braking systems, preventing overheating.
Moreover, wire mesh’s robustness makes it ideal for applications requiring durability under a wide range of conditions. In off-road and heavy-duty vehicles, wire mesh is frequently used in the reinforcement of vehicle components exposed to harsh environments. Its corrosion resistance, particularly in stainless steel variants, ensures longevity and reliable performance, qualities critically important in heavy-duty contexts.
wire mesh automotive
As automotive manufacturers continue to focus on sustainability, wire mesh aligns perfectly with eco-friendly goals. Its recyclability and ease of repurposing fit seamlessly into the circular economy model, reducing the environmental impact associated with automotive production. Additionally, the lightweight nature of wire mesh contributes to overall vehicle weight reduction, aiding in lowering fuel consumption and subsequent carbon emissions.
Expertise in selecting the appropriate type of wire mesh for specific applications is crucial for achieving the optimal balance between weight, strength, and cost. Automotive engineers and material scientists are pivotal in this process, drawing on empirical research and testing to validate the performance characteristics of wire mesh under various conditions. Their work ensures that each application meets the rigorous safety and performance standards set by the automotive industry.
The authority of wire mesh as a critical component in automotive engineering is well-documented in industry journals and patents. Leading automotive manufacturers have published numerous case studies and technical papers validating its efficacy and detailing advancements in wire mesh production and applications. These documents serve as valuable resources for engineers seeking to understand and leverage wire mesh technology further.
Lastly, trustworthiness is fundamental in the use of wire mesh within the automotive sector. The material’s proven track record in improving vehicle safety and performance has led to strong endorsements from industry experts. Rigorous testing by independent organizations further bolsters confidence in its reliability under real-world conditions. Automotive producers’ transparent communication regarding the benefits and limitations of wire mesh applications enhances consumer trust and confidence in these vehicles.
In conclusion, wire mesh proves to be an indispensable material in the automotive industry, satisfying multifaceted roles across vehicle systems and components. Its applications extend beyond mere functionality, contributing significantly to design, safety, and sustainability. As the industry drives towards increasingly complex and environmentally conscious solutions, wire mesh remains at the forefront, underscoring its expert-reputed prominence and trusted reliability in automotive manufacturing.