In the intricate world of woven wire screen manufacturing, a blend of technical precision, material expertise, and cutting-edge innovation sets leading manufacturers apart. The demand for premium woven wire screens continues to soar across industries like mining, agriculture, petrochemical, and wastewater treatment, where these products play a pivotal role in sorting, filtering, and safeguarding processes. Yet, with numerous suppliers vying for prominence, distinguishing genuine expertise and reliability becomes crucial to ensuring superior product performance and longevity.
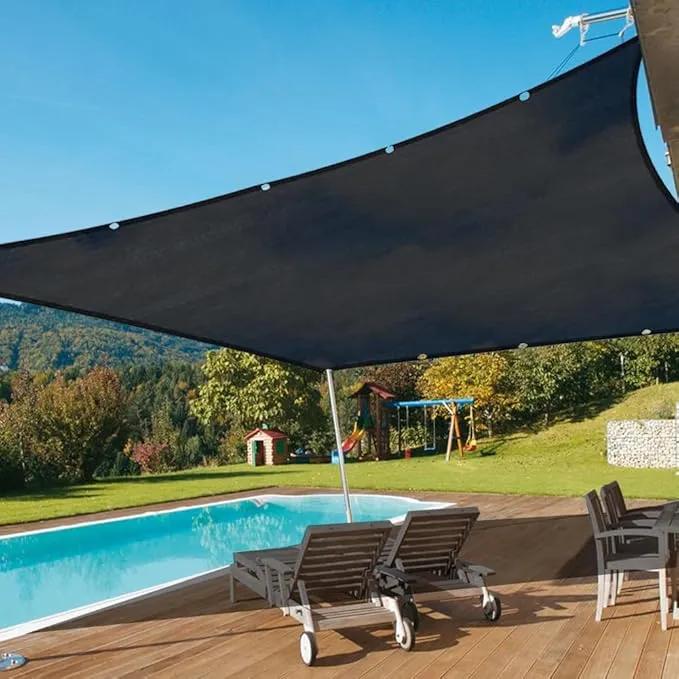
Woven wire screens are esteemed for their versatility and robustness, crafted from materials such as high carbon steel, stainless steel, brass, and other specialized alloys. Each type of material is chosen for its unique properties that suit specific industrial applications. For instance, stainless steel woven wire screens are immensely popular in industries requiring corrosion resistance and longevity, such as food processing and pharmaceuticals. Conversely, high carbon steel is preferred for its tensile strength in heavy-duty applications like mining.
Renowned woven wire screen manufacturers invest heavily in state-of-the-art technology to enhance product integrity and precision. Advanced weaving techniques ensure that each wire screen boasts uniformity in mesh size and wire length, critical factors that influence the screen’s performance in filtering and separation processes. This technological prowess often extends to automated quality checks, which detect irregularities and guarantee that each wire screen upholds stringent industry standards.
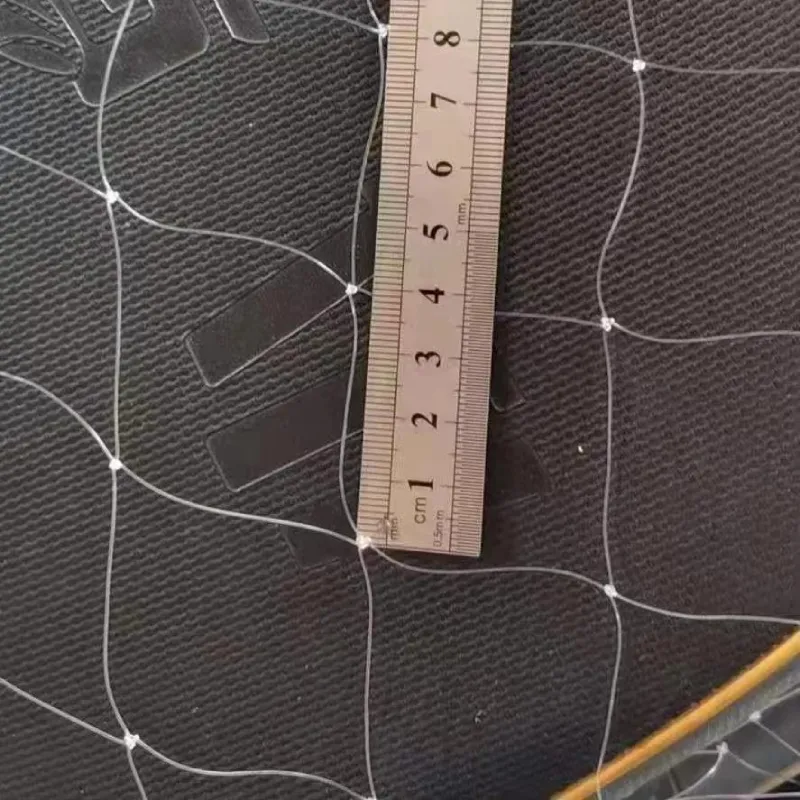
Expertise in custom manufacturing also defines leading manufacturers. Recognizing that no two applications are identical, they offer bespoke solutions tailored to unique operational needs. This involves meticulous consultations where engineers collaborate with clients to design screens with specific mesh apertures, wire diameters, and materials. Such bespoke manufacturing ensures the wire screens not only meet but surpass operational demands, thus optimizing efficiency and efficacy in their respective applications.
In addition to technical precision, environmental considerations now play an essential role in the manufacturing and application of woven wire screens. Manufacturers dedicated to sustainable practices utilize eco-friendly processes, reducing waste, and optimizing resource usage. Many have adopted recycling initiatives, allowing clients to return used wire screens for refurbishment or material recycling, thereby minimizing the environmental footprint of their operations.
woven wire screen manufacturers
Authoritativeness in this field is often demonstrated through industry certifications and compliance with international standards. Key certifications, such as ISO 9001 for quality management systems, underline a manufacturer’s commitment to excellence. Adherence to these standards not only promotes trust but also ensures that products are universally recognized for their quality, safety, and efficacy.
Establishing trustworthiness among woven wire screen manufacturers hinges upon transparent communication and reliable after-sales service. Leading manufacturers provide comprehensive documentation, including material certifications and product guides, to educate and reassure clients. Furthermore, they extend robust support services, often including installation guidance, maintenance tips, and readily available technical support, which reinforces client confidence and loyalty.
In choosing a woven wire screen manufacturer, consider those with an illustrious track record, a commitment to innovation, and unwavering adherence to quality. Peer reviews and industry awards further solidify a manufacturer’s reputation, offering a clearer picture of their market standing. Ultimately, the right manufacturer not only provides superior woven wire screens but also partners with clients to advance operational efficiency and sustainability goals.
When navigating the complex landscape of woven wire screen manufacturing, prioritize those whose dedication to expertise, innovation, and client satisfaction is evident. By doing so, you secure a partner in production who equips you with the tools to excel in demanding industrial environments.